General Information
- Type of industry: Paper and Pulp
- Type of production: Corrugated packaging
- Technology involved: Four-cylinder piston compressor type 4KoK7 from Spilling Technologies
Partners involved
Demo-site location
The application: Smurfit Kappa
Smurfit Kappa (SK) is a renowned FTSE 100 company and a global leader in paper-based packaging solutions. With operations in 22 European countries and 13 countries in the Americas, Smurfit Kappa has established itself as a key player in the industry. The company is committed to sustainability and energy conservation, aiming to reduce emissions by 60% by 2030.
Smurfit Kappa (SK) Morava plant is one of the many paper mills belonging to the SK Group and it is located in Czech Republic. This paper mill has a very long history: founded in 1891 by Mr. Carl Weisshuhn, in 1946 it became and stayed a state-owned company until 1993 when it was privatised. A year later a new paper machine was built (the same currently in use) and in 1996, the plant was acquired by Smurfit Kappa that, through a series of investments, increased its output from the original 35 kT/year to 76 kT/year.
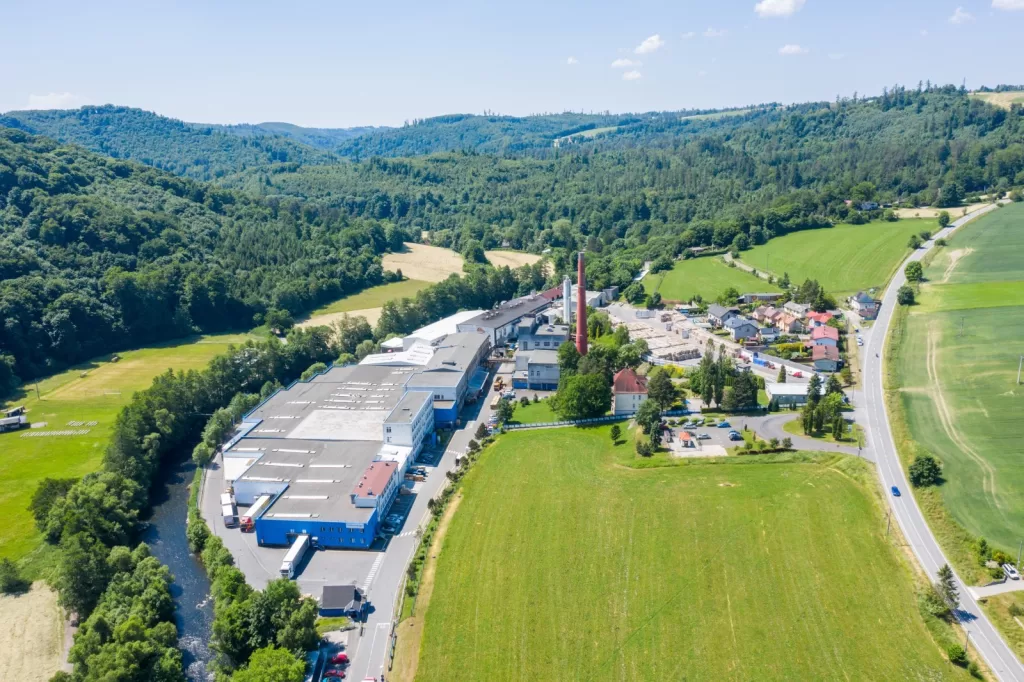
Production site of Smurfit Kappa in Morava, Czech Republic
In order to develop its corrugated packaging solutions, SK puts in place a production process that drains the paper in three sections:
- Wire section
- Press section
- Drying section
Within the SPIRIT Project, Smurfit Kappa will integrate a heat pump in the drying process. The plant’s drying section consists of 36 drying cylinders full of five bar steam. Steam is supplied to the process by a boiler house burning natural gas and a small percentage of biogas.
The heat pump will optimize the use of steam in the drying process and the Spilling four-cylinder piston compressor will compress this steam above 5 bars and send it back to the drying process. A new separator will also be implemented along the condensation path, evaporating low-pressure steam from the condenser. This steam will then be compressed and reintroduced into the paper production process.
The implementation of the SPIRIT project offers several advantages to the Smurfit Kappa Morava Paper Plant, including:
- Clean steam production: the heat pump system enables the production of up to 0.7 t/h of steam from condensation using an electrical method.
- Steam savings and CO2 emissions reduction: the heat pump system generates the steam which would otherwise be generated using natural gas and biogas.
- Improved boiler efficiency: the reduction in condensate temperature achieved through the SPIRIT project enhances the overall efficiency of the boilers, resulting in energy savings.
The technology: Spilling Technologies
The steam compressor to be supplied by Spilling Technologies and installed at Smurfit Kappa, is a 4-cylinder piston compressor unit installed in a container.
Knowledge Provider: German Aerospace Center
The German Aerospace Center (DLR) founded the institute of Low-Carbon Industrial Processes (DLR-DI) in 2019 aiming for vital contributions to decarbonize energy-intensive industrial sectors (e.g. food and paper industry). Currently, the DLR-DI is developing two to prototypes of high temperature heat pumps based on the Rankine and Brayton cycle. The results and findings of those prototypes can be transferred directly to the SPIRIT Project. Within the scope of the SPIRIT project, the DLR has a coordinating role by managing the communication between the end user and the technology provider, ensuring that project goals are met. Furthermore, the DLR delivers technical input to the partners by taking lead in developing the P&ID for the demonstrator. The basic engineeringp hase, is led by the DLR as well as the demonstration and monitoring activities of the demonstration cases. Furthermore, the DLR is in charge of the development of modular concepts for heat pumps, and the combined technology portfolio.