The steam compressor to be supplied by Spilling Technologies and installed at Smurfit Kappa, is a 4-cylinder piston compressor unit installed in a container.
Spilling is manufacturer of large-scale, tailor-made steam compressors since decades. The new technology is a standardised container version, foreseen for simpler planning and “plug and play” installation. It shall be the prototype for a serial-production of the unit in the future, which will enable cost reduction for its manufacturing. Additionally, this type shall cover a larger field of small to medium-sized thermal power applications, where the large, tailor-made Spilling compressors are too big to be installed (e.g. in the medium-sized food and pharmaceutical sectors).
In light of this, for this demonstration site, a smaller-scaled compressor type has been chosen to fit into a standard 20” container allowing for easier transport and installation. The container shall be completely equipped with control panel, frequency converter, condensate injection system, draining etc., as well as all necessary piping, wiring, thermal insulation and noise insulation.
Finally, there are three lines for different pressure ranges foreseen, like follows:
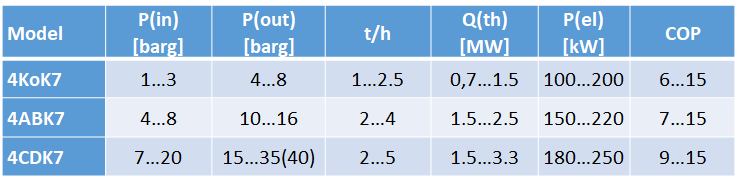
4-cylinder-units of the Spilling K7-type
The compressor unit at Smurfit Kappa will be one of the low-pressure line 4KoK7, compressing exhaust) flash steam from condensate expansion of up to 1,0 t/h steam flow rate (~700 kWth) from 2 barabs to 6 barabs. The compression takes place as single stage compression, so all 4 cylinders at the compressor unit will be operating in parallel. The outcoming steam will be cooled to max. 180°C by condensate injection. By this the steam flow rate at the outlet side increases even for about 8%.
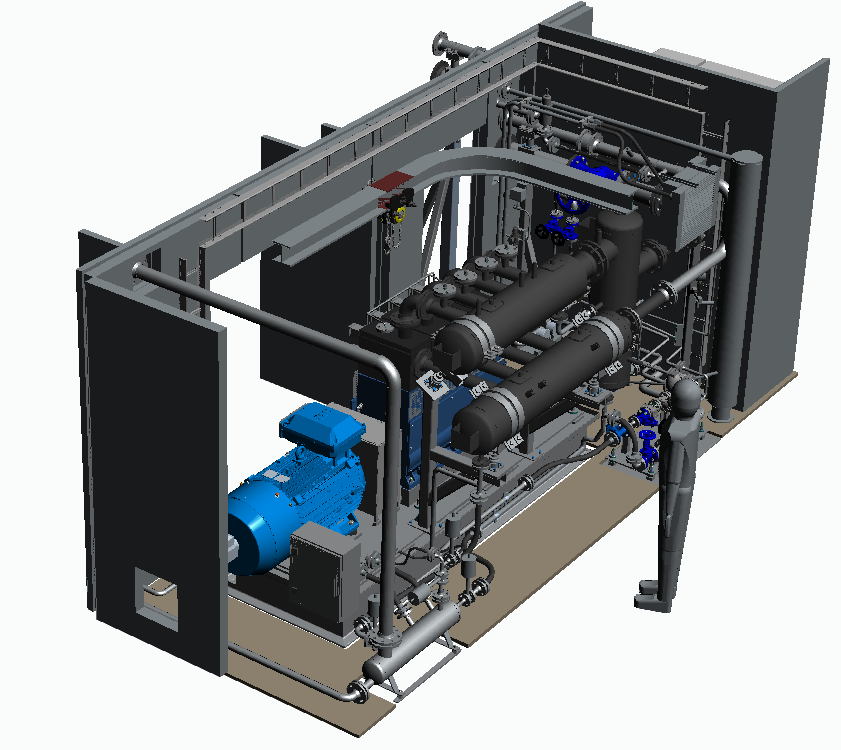
Draft for container installation
The advantages of this type of Spilling compressor are: its high efficiency and its wide control range of about 25-100% mass flow rate. Also in part load the compressor can be operated with the same good efficiency like at full load, meaning that its electrical power consumption is simply proportional to the flow rate.
Generally, single stage compressors like foreseen here can compress the steam to pressures by up to factor 3 (e.g. from 2 to 6 barabs or from 4 to 12 barabs). For higher inlet pressures the max. compression ratio becomes certainly smaller.