The heat pump to be delivered by Mayekawa and installed at Stella Polar consists of a cascade system based on two cycles that use ammonia and a hydrocarbon (Pentane) as working fluids, respectively. Mayekawa has prioritised the development of heat pumps using natural working media with low GWP, which ensures a truly sustainable and future-proof technology for industry.
Bottom Cycle Ammonia Heat Pump
The bottom cycle ammonia heat pump is based on commercially available technology from Mayekawa which is normally used for hot water production in food and district heating sectors. Mayekawa has developed a portfolio of piston and screw compressors to meet the demands (namely high temperature and high pressure) of ammonia applications. For this application, a piston compressor was chosen due to its intrinsically high compression efficiency and low heat losses which act to maximise the overall system efficiency.
Heat is supplied to this bottom cycle at 21°C from the existing ammonia based freezing plant. The evaporator of the ammonia heat pump acts as the new condenser in the freezing plant. It is installed in parallel to the existing condenser to maximise efficiency of the overall system. A flooded evaporator cycle configuration is therefore chosen to mitigate the response of the system to source heat fluctuations. The ammonia heat pump upgrades the heat from the freezing plant to produce 501 kW at a temperature of 82°C which can be supplied to the top cycle pentane heat pump.
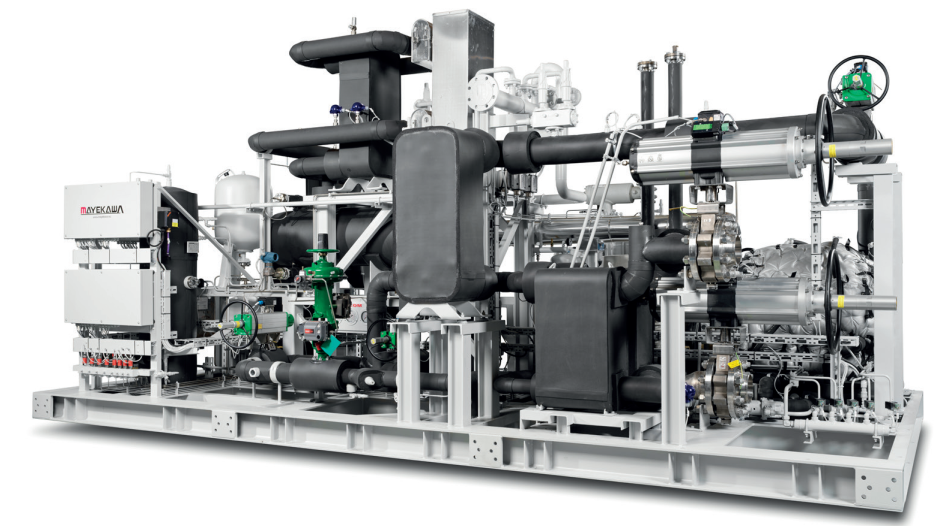
Mayekawa ammonia heat pump
The top cycle pentane heat pump is one of the innovative components of the system. The compressor and heat pump package is specifically developed to replace the use of conventional fossil fuelled burners for production of steam.
The heat pump uses conventional oil-lubricated screw compressor technology, with some minor modifications to the compressor to meet the high temperature requirements of the system. Further innovations to deal with high temperatures are present within the oil system. Namely, the bearing oil lubrication is a separate closed loop system maintained at lower temperatures with a focus on degassing the oil before supplying it to the compressor bearings. The oil injection circuit is a conventional oil lubrication cycle designed in order to recover the oil from the discharge gas and resupply it to the compressor rotors for optimal efficiency on the gas compression.
The source heat from the bottom cycle heat pump is supplied to the top cycle heat pump at 82°C leading to an evaporating temperature of the Pentane medium of 78°C. Once again, a direct coupling is made between the bottom and top cycle to maximise the system efficiency and a flooded configuration is chosen to mitigate the system fluctuations. The heat pump upgrades the heat to 150°C with a heating capacity of 717 kW to produce 4 barabs saturated steam which can cover the demand of the prawn cooker on site.
The technology is expected to become commercially available in 2025, with the SPIRIT project playing an important role in the development and validation of the technology as a reliable product.
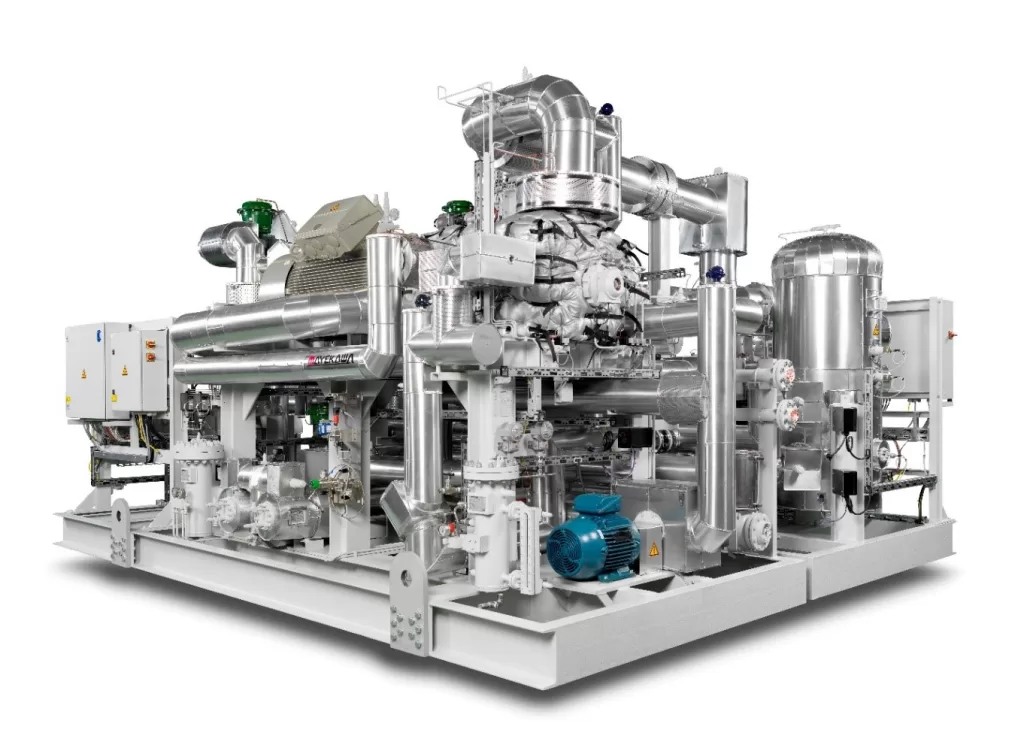
First prototype of pentane heat pump developed by Mayekawa for steam production